FAMU-FSU researchers design cryogenic hydrogen storage and delivery system for next-generation aircraft
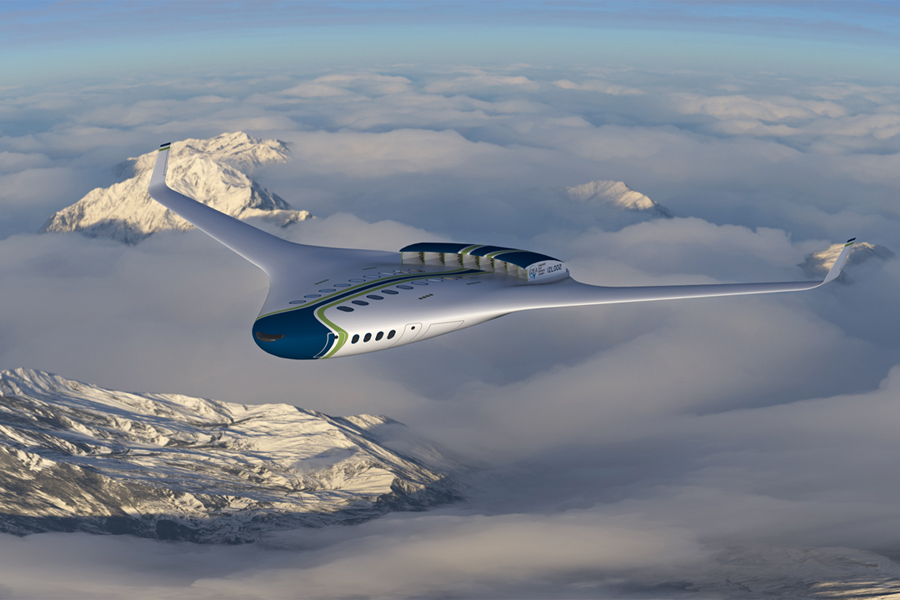
Researchers at the FAMU-FSU College of Engineering have designed a liquid hydrogen storage and delivery system that could help make zero-emission aviation a reality. Their work outlines a scalable, integrated system that addresses several engineering challenges at once by enabling hydrogen to be used as a clean fuel and also as a built-in cooling medium for critical power systems aboard electric-powered aircraft.
The study, published in Applied Energy, introduces a design tailored for a 100-passenger hybrid-electric aircraft that draws power from both hydrogen fuel cells and hydrogen turbine-driven superconducting generators. It shows how liquid hydrogen can be efficiently stored, safely transferred and used to cool critical onboard systems — all while supporting power demands during various flight phases like takeoff, cruising, and landing.
“Our goal was to create a single system that handles multiple critical tasks: fuel storage, cooling and delivery control,” said Wei Guo, a professor in the Department of Mechanical Engineering and corresponding author of the study. “This design lays the foundation for real-world hydrogen aviation systems.”
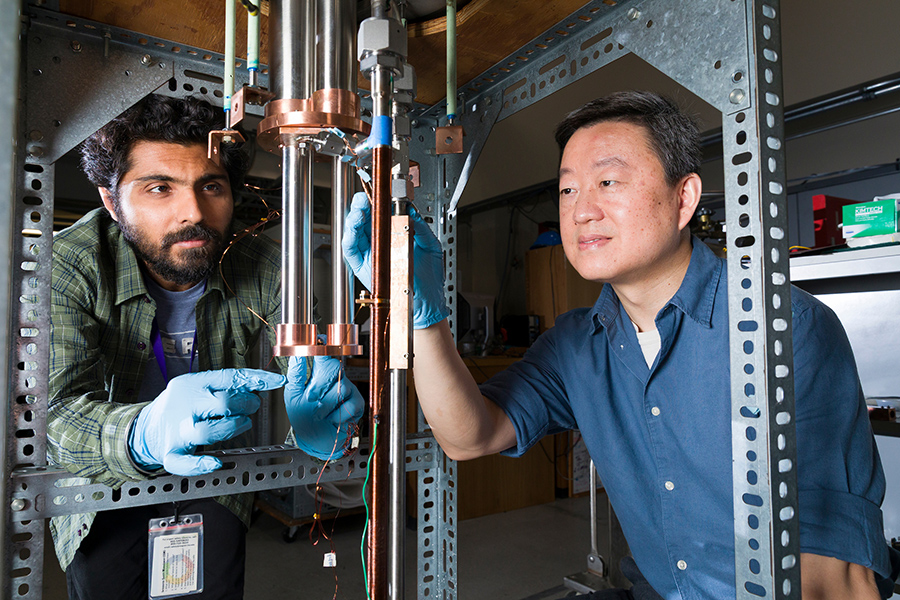
WHAT THEY DID
Hydrogen is seen as a promising clean fuel for aviation because it packs more energy per kilogram than jet fuel and emits no carbon dioxide. But it’s also much less dense, meaning it takes up more space unless stored as a super-cold liquid at –253°C.
To address this challenge, the team conducted a comprehensive system-level optimization to design cryogenic tanks and their associated subsystems. Instead of focusing solely on the tank, they defined a new gravimetric index, which is the ratio of the fuel mass to the full fuel system. Their index includes the mass of the hydrogen fuel, tank structure, insulation, heat exchangers, circulatory devices and working fluids.
By repeatedly adjusting key design parameters, such as vent pressure and heat exchanger dimensions, they identified the configuration that yields the maximum fuel mass relative to total system mass. The resulting optimal configuration achieves a gravimetric index of 0.62, meaning 62% of the system’s total weight is usable hydrogen fuel, a significant improvement compared to conventional designs.
The system’s other key function is thermal management. Rather than installing a separate cooling system, the design routes the ultra-cold hydrogen through a series of heat exchangers that remove waste heat from onboard components like superconducting generators, motors, cables and power electronics. As hydrogen absorbs this heat, its temperature gradually rises, a necessary process since hydrogen must be preheated before entering the fuel cells and turbines.
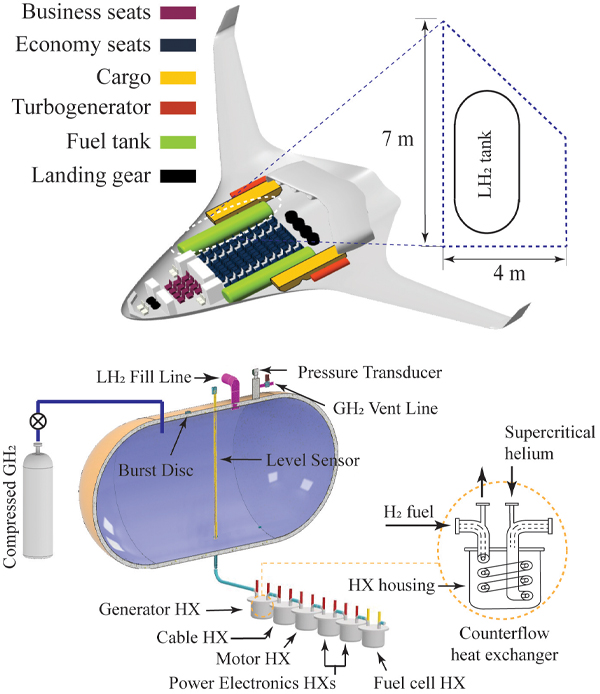
HOW IT WORKS
Delivering liquid hydrogen throughout the aircraft presents its own challenges. Mechanical pumps add weight and complexity and can introduce unwanted heat or risk failure under cryogenic conditions. To avoid these issues, the team developed a pump-free system that uses tank pressure to control the flow of hydrogen fuel.
The pressure is regulated using two methods: injecting hydrogen gas from a standard high-pressure cylinder to increase pressure and venting hydrogen vapor to decrease it. A feedback loop links pressure sensors to the aircraft’s power demand profile, enabling real-time adjustment of tank pressure to ensure the correct hydrogen flow rate across all flight phases. Simulations show it can deliver hydrogen at rates up to 0.25 kilograms per second, sufficient to meet the 16.2-megawatt electrical demand during takeoff or an emergency go-around.
The heat exchangers are arranged in a staged sequence. As the hydrogen flows through the system, it first cools high-efficiency components operating at cryogenic temperatures, such as high-temperature superconducting generators and cables. It then absorbs heat from higher-temperature components, including electric motors, motor drives and power electronics. Finally, before reaching the fuel cells, the hydrogen is preheated to match the optimal fuel cell inlet conditions.
This staged thermal integration allows liquid hydrogen to serve as both a coolant and a fuel, maximizing system efficiency while minimizing hardware complexity.
“Previously, people were unsure about how to move liquid hydrogen effectively in an aircraft and whether you could also use it to cool down the power system component,” Guo said. “Not only did we show that it’s feasible, but we also demonstrated that you needed to do a system-level optimization for this type of design.”
FUTURE STEPS AND COLLABORATORS
While this study focused on design optimization and system simulation, the next phase will involve experimental validation. Guo and his team plan to build a prototype system and conduct tests at FSU’s Center for Advanced Power Systems.
The project is part of NASA’s Integrated Zero Emission Aviation program, which brings together institutions across the U.S. to develop a full suite of clean aviation technologies. Partner universities include Georgia Tech, Illinois Institute of Technology, University of Tennessee and University at Buffalo. FSU leads the effort in hydrogen storage, thermal management and power system design.
At FSU, key contributors include graduate student Parmit S. Virdi; professors Lance Cooley, Juan Ordóñez, Hui Li, Sastry Pamidi; and other faculty experts in cryogenics, superconductivity and power systems.
FUNDING
This project was supported by NASA as part of the organization’s University Leadership initiative, which provides an opportunity for U.S. universities to receive NASA funding and take the lead in building their own teams and setting their own research agenda with goals that support and complement the agency’s Aeronautics Research Mission Directorate and its Strategic Implementation Plan.
Guo’s research was conducted at the FSU-headquartered National High Magnetic Field Laboratory, which is supported by the National Science Foundation and the State of Florida.
The post FAMU-FSU researchers design cryogenic hydrogen storage and delivery system for next-generation aircraft appeared first on Florida State University News.